Freeze Applications
Freeze applications are commonly used in situations where there is no other practical means of containing pressure to replace damaged equipment or to gain well access without killing the well. It is an inexpensive and safe way to control well pressures when removal of the wellhead, pipeline or auxiliary equipment is required as part of a maintenance or repair procedure.
We have years of experience in freeze applications for a wide range of situations with pressures of up to 7,500 Psi. We know that the safety of any freeze application is directly related to experience – our team is the most highly trained and skilled you will find in the industry.
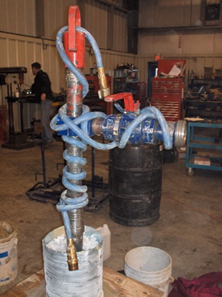
Typical Freeze Application Process:
Basic description of freeze plugging:
Our freeze plugging system consists of injecting a thick slurry of water-based bentonite gel and applying a refrigerant to the target area to freeze the gel to form an ice plug.
The gel that is injected is of similar viscosity to peanut butter.
The bentonite slurry is sticky enough to bond to tubulars and wellhead components and viscose enough to hold the medium in place until frozen. The bentonite clay also adds structure to the ice plug in that the particles interrupt the fracture paths that would be found in pure water ice that is inherently brittle. We routinely pressure test the ice plugs to full working pressure of the equipment that we are working on and commonly install ice plugs to contain well pressures exceeding 40Mpa.The methods used depend on what the area to be frozen contains or has contained or whether there is a leak to atmosphere from the area to be frozen. Pressure testing is performed to 1 ½ times the surface pressure of the well, or to the maximum well head pressure rating.
Our refrigerant of choice is solid CO2 (dry ice) because it is easy to handle, transport, and apply to the wellhead; it also makes it easier to control the target equipment temperature.
Bentonite Gel:
Our freeze plugging system consists of injecting a thick slurry of water-based bentonite gel and applying a refrigerant to the target area to freeze the gel to form an ice plug.
The gel that is injected is of similar viscosity to peanut butter.
The bentonite slurry is sticky enough to bond to tubulars and wellhead components and viscose enough to hold the medium in place until frozen. The bentonite clay also adds structure to the ice plug in that the particles interrupt the fracture paths that would be found in pure water ice that is inherently brittle. We routinely pressure test the ice plugs to full working pressure of the equipment that we are working on and commonly install ice plugs to contain well pressures exceeding 40Mpa.The methods used depend on what the area to be frozen contains or has contained or whether there is a leak to atmosphere from the area to be frozen. Pressure testing is performed to 1 ½ times the surface pressure of the well, or to the maximum well head pressure rating.
Applications
Bentonite viscosifier is used in most cement slurries to decrease slurry weight and increase slurry volume. In bentonite-cement diesel-oil (BCDO) and bentonite diesel-oil (BDO) slurries, bentonite forms a thick, paste-like material that helps prevent lost circulation.
Compatibility
Bentonite is compatible with slurries containing fibrous, granular, and flake-type lost-circulation materials.
Benefits
Bentonite can provide the following benefits:
- It is easily obtained and can be an effective lost- circulation material when mixed with other common oilfield materials.
- The overall cost for treatment can be less than that of other lost-circulation methods.
- This material can be effective in regular and cavernous lost-circulation zones and where drilling with fibrous, granular, or flake materials has been ineffective
Diagram of Freeze Application:
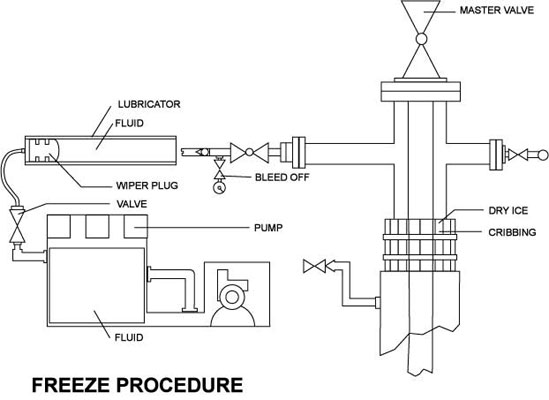
Snubco Domestic Freeze Unit Specifications:
- North America: Truck Mounted Mobile International 4900 Series 466E with positive shutdown diesel engine c/w 22’ insulated heating van. Pumping capabilities to 7500 Psi. Fully self-contained
- All equipment meets NACE specifications.
- We use Proheat, an intrinsically safe electric heating system for maintaining thaw at the pumping and pressure monitoring area
Although the freeze procedure remains essentially the same as the first time it was utilized in the 1920’s, equipment design to accomplish the job has evolved significantly. Snubco currently offers three different styles of freeze equipment
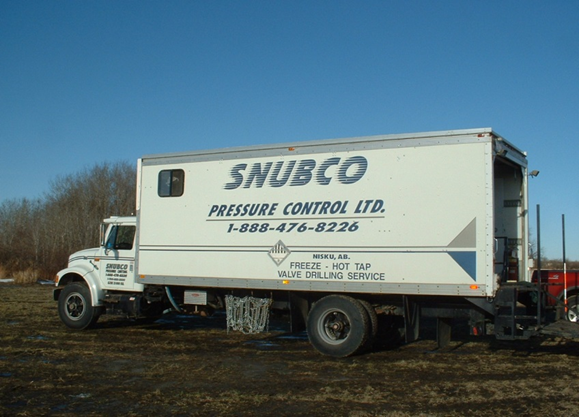

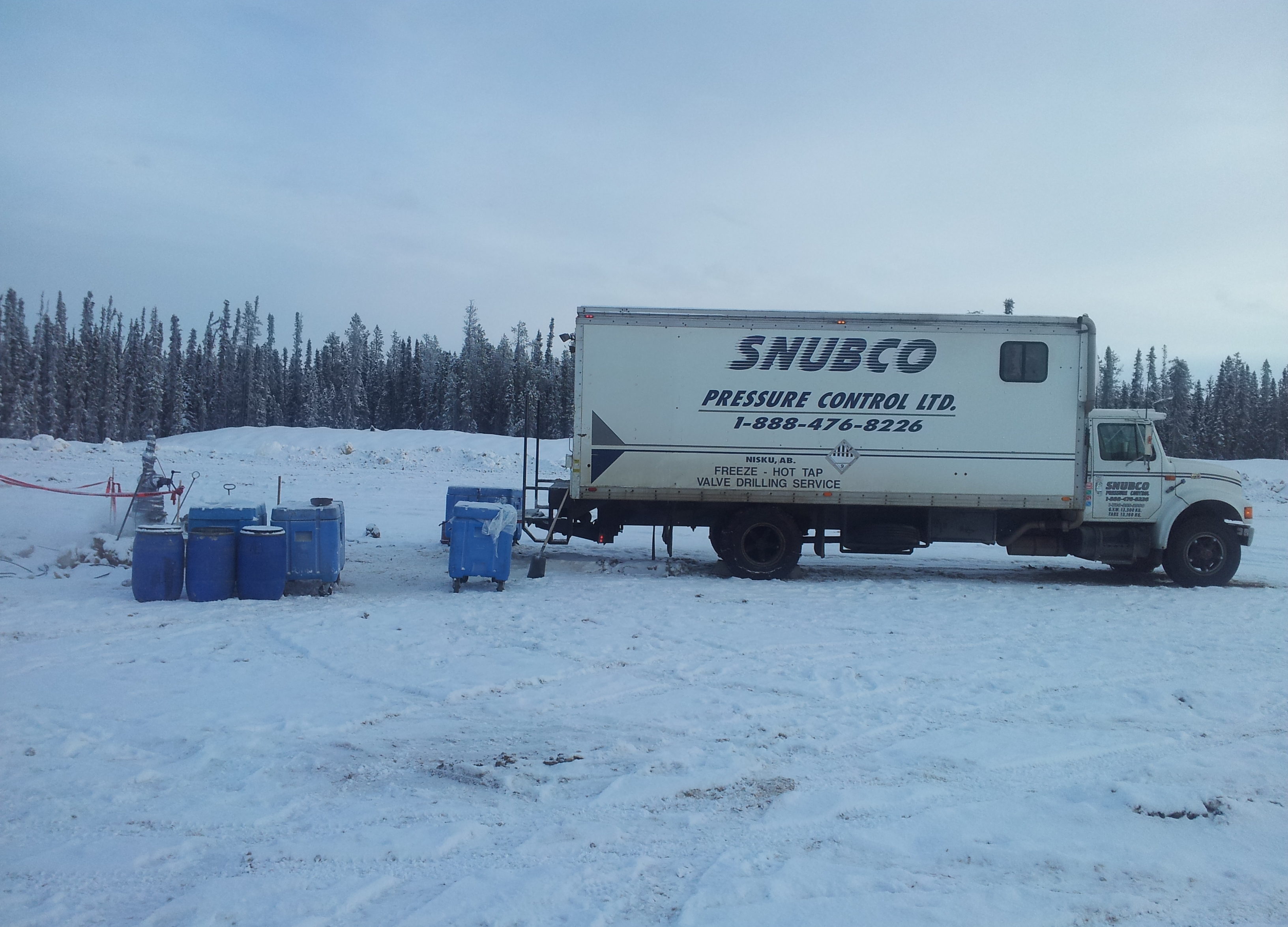
Snubco Freeze Equipment Designs:
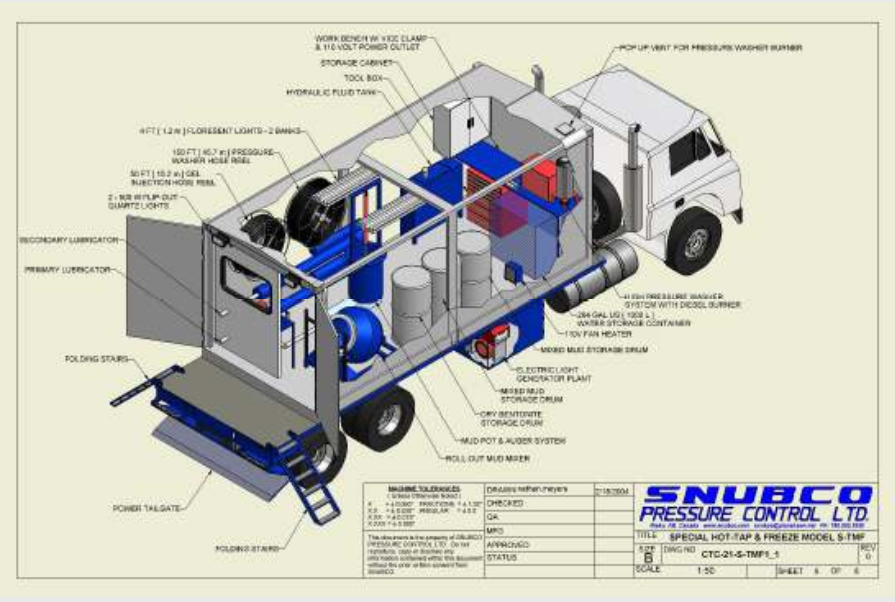
Truck mounted automated injection system
- Unit is completely self-reliant for freeze work (with the exception of dry ice production)
- Highly mobile for quick dispatch
- Retains all of the abilities of the Model S-CF sea-container freeze unit
- All hydraulic functions power take pff (PTO) mounted
- Power tailgate to facilitate loading of heavy articles into van body
- Variety of cab and chassis available to suit customer needs
- Van body insulated and heated for operations in cold environments
- Van body available in several sizes to suit customer needs. 7500 Psi [51 Mpa/517 Bar]
- Automated injection system
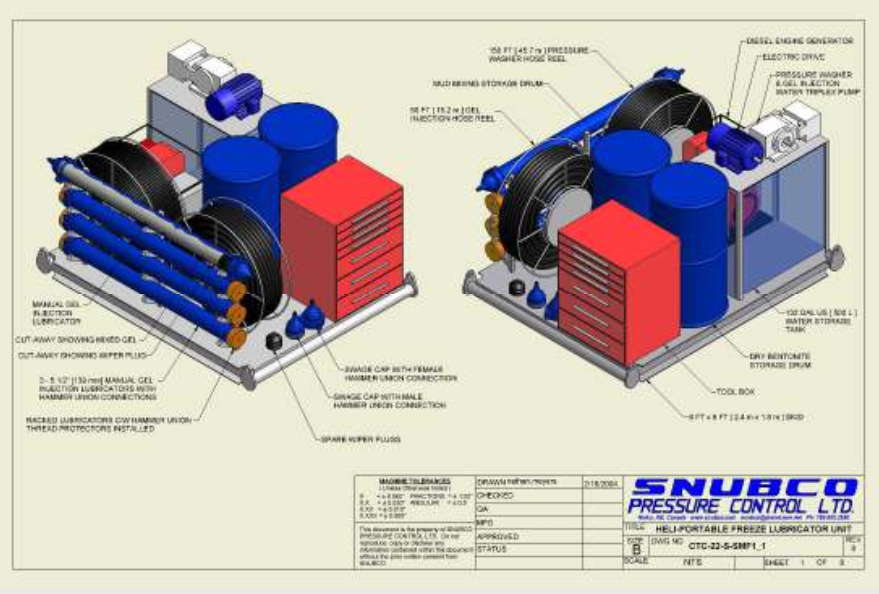
Heli-portable Lubricator Freeze System
- Highly portable design for remote area and offshore operations
- Maximum pumping pressures of 3000 Psi [21 Mpa/206 Bar]
- Low capital cost
- Simple, robust design
- Onboard pumping system
- Onboard generator for pumping and mixing operations
- 5000 Psi [35 Mpa/343 Bar] gel injection check valve
- 50’ [15 M] x 5000 Psi [35 Mpa/343 Bar] gel injection hose
- Manual gel mixing system
- 3000 Psi [21Mpa/206 Bar]
- Lubricator System
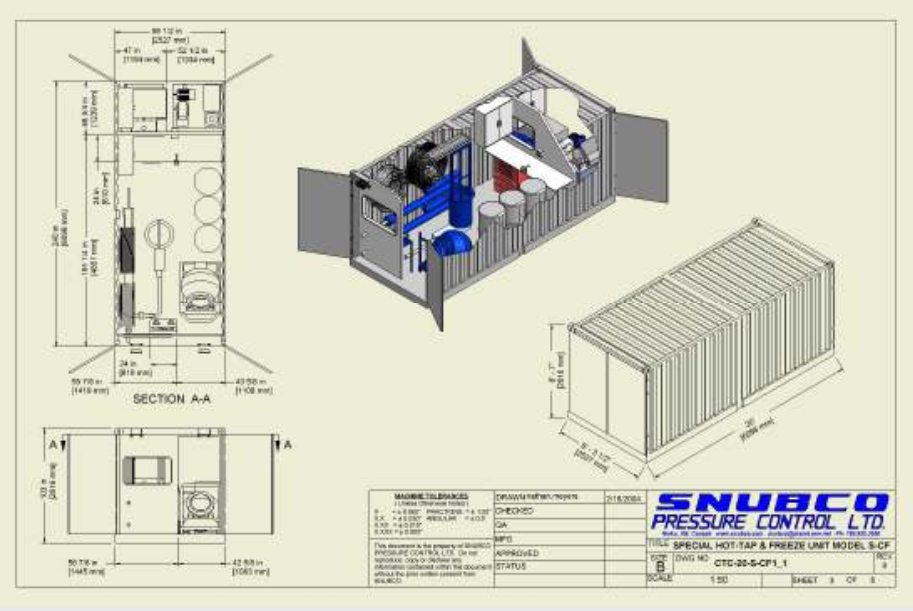
Sea-Container Automated Injection System
- Entire unit installed within a standard 20’ [6.09 m] sea container
- Onboard gel injection system rated to 7500 psi [51 Mpa/517 Bar] injection pressure
- Dual gel injector system provides redundancy
- Integral intensifiers to allow lower hydraulic working pressures on injectors
- Onboard automated injection lubricator gel filling system
- 10,000 psi [70 Mpa/680 Bar] gel injection manifold
- 10,000 psi [70 Mpa/680 Bar] x 50’ [15 M] injection hose
- 10,000 psi [70 Mpa/680 Bar] gel injection check valve
- Freeze gel mixing equipment wheel mounted to facilitate outside mixing
- Onboard diesel generator for driving hydraulic and electrical systems
- Heated pressure washer for thawing and cleaning operations c/w hose and wand
- 260 gallon [1000 L] water tank for gel mixing and pressure washer operations
- Inside fluorescent lighting
- Outside quartz lighting
- Work bench and storage compartments
- Wet and dry bentonite gel storage
- Optional inside electrical heating system7500 Psi [51 Mpa/517 Bar]
- Automated Injection System